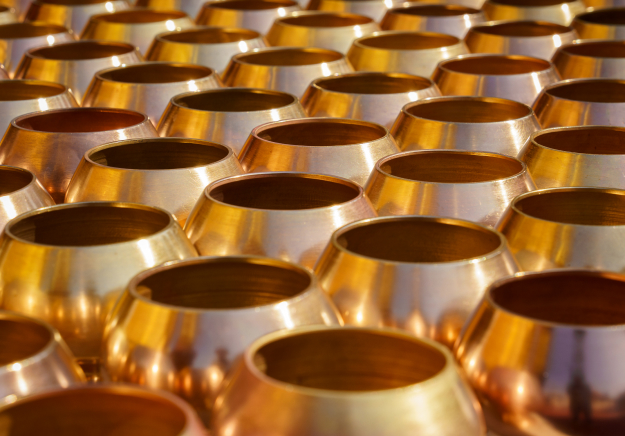
Enhancing Metal Durability and Preparation
Phosphating is a critical process in the metalworking sector, where metal surfaces are coated with phosphate. This procedure is essential for preparing metal components for final operations like powder coating or painting.
Speak to our expertsKey Benefits:
-
Defining Phosphating
Phosphating is the chemical reaction that occurs when a metal surface interacts with a diluted phosphoric acid solution. This interaction transforms the metal surface into a phosphate coating, achieved by immersing the component in a solution containing metal ions like iron, zinc, or manganese.
-
Phosphating Procedure in Detail
Pretreatment
The metal surface must be thoroughly cleaned before applying the phosphate coating. Removing oils, grease, and other contaminants is necessary for the phosphate to properly adhere to the metal.
Phosphate Coating Application
After cleaning the metal, it is immersed in the phosphating solutions. Careful control of the solution composition, temperature, and immersion time is essential to achieve the desired coating thickness and crystal size.
Post Treatment
Once the desired phosphate coating is achieved, metal parts are rinsed with water to remove residual phosphating solutions. The metal parts are then dried, readying them for subsequent finishing processes like powder coating or painting.
Phosphate Layer Sealing
Depending on the application, the sealant can be a chromate, a passivation, or a lubricant.
At Sona SPEED, we leverage our expertise in the design, development, and realization of space-grade motors, such as Brushless DC motors and permanent magnet & hybrid stepping motors, to ensure the highest quality phosphating process for our products. Our commitment to excellence and innovation sets us apart in the industry.
Speak to our experts
-
Phosphating's Contemporary Significance
In today's world, phosphating holds a pivotal role in industries such as construction, automotive, and aerospace. It readies metal surfaces for demanding applications, a crucial aspect as we navigate global supply chains and cater to the growing needs for durability and longevity.
-
Varieties of Phosphating Processes:
Iron Phosphating
Results in a light or medium phosphate coat, offering moderate corrosion protection and serving as a primer for additional coatings.
Zinc Phosphating
Provides a thicker coating than iron phosphating, leading to improved paint adhesion and enhanced corrosion resistance. Commonly used in industries requiring corrosion protection, such as automotive and military.
Manganese Phosphating
Produces a heavy and durable phosphate coat with excellent wear resistance. Often applied to high-wear parts like bearings and gears.
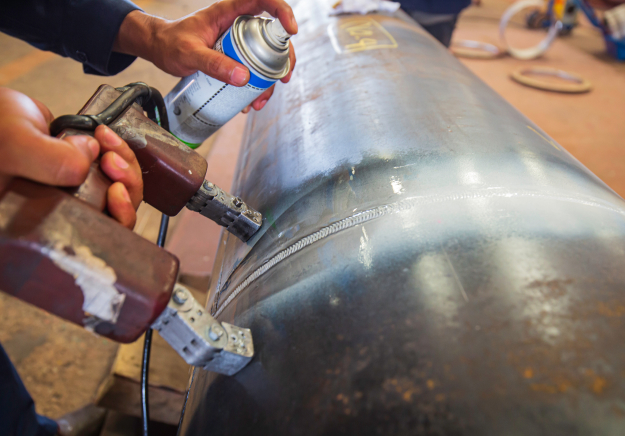