Expert Chromic Anodising Solutions with Sona SPEED
At Sona SPEED, we specialize in providing high-quality Chromic Anodising solutions tailored for Aerospace, Defence, Marine, and other high-performance industries. Our expertise in precision engineering and surface treatment ensures that your components receive the highest level of protection and performance.
Speak to our expertsWhat is Chromic Anodising?
Chromic Anodising is a specific type of anodising process that uses chromic acid as the electrolyte. This method creates a thin, yet highly effective, protective oxide layer on aluminium and its alloys. Chromic Anodising is particularly valued for its ability to protect complex and delicate components without compromising their dimensional stability.
Why Choose Chromic Anodising?
Chromic Anodising is preferred in industries where maximum protection is required with minimal impact on the material's mechanical properties. Its thinner coating ensures that the material's surface integrity and tolerances are maintained, making it ideal for components that require precise fits and finishes.
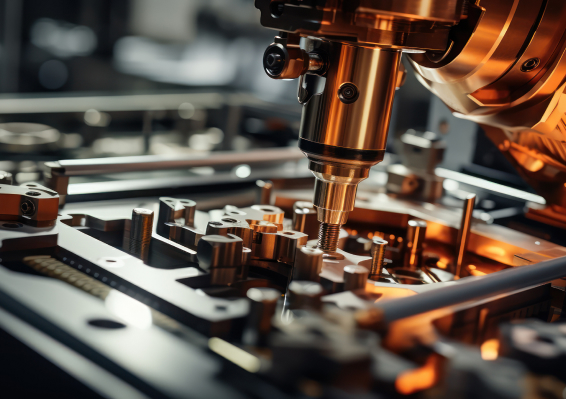
Applications of Chromic Anodising in Industries:
-
Aerospace
-
Defence
-
Marine
-
Industrial
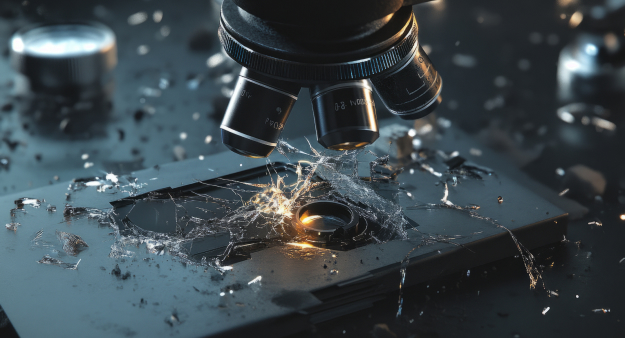
Key Features of Chromic Anodising:
-
Superior Corrosion Resistance
Provides exceptional protection against corrosion, especially in environments with high moisture or chemical exposure.
-
Thin Coating
The process creates a thin yet highly protective layer, ensuring that the dimensional integrity of delicate components is preserved.
-
Non-Reflective Surface
Chromic Anodising produces a non-reflective, matte finish that is particularly useful in military and aerospace applications.
-
High Compatibility
Ideal for use with aluminium alloys, including high-strength and specialty grades.
-
Enhanced Adhesion
The anodised surface offers improved adhesion for paint and other coatings, ensuring longer-lasting finishes.
Our Chromic Anodising Process:
-
Superior Corrosion Resistance
The component is thoroughly cleaned and prepared to ensure optimal coating adhesion and uniformity.
-
Chromic Anodising
The material is immersed in a chromic acid solution, where an electric current is applied to form the anodic layer.
-
Sealing
The anodised surface is sealed to enhance corrosion resistance and durability.
-
Inspection & Quality Control
Every component undergoes rigorous testing and inspection to ensure it meets industry standards and customer specifications.
-
Enhanced Adhesion
The anodised surface offers improved adhesion for paint and other coatings, ensuring longer-lasting finishes.
Why Partner with Sona SPEED?
Sona SPEED provides industry-leading anodising services with a focus on quality, precision, and reliability. Our Chromic Anodising solutions are backed by years of experience and cutting-edge technology, ensuring that your components receive the protection they need to perform in the most demanding environments.
Speak to our experts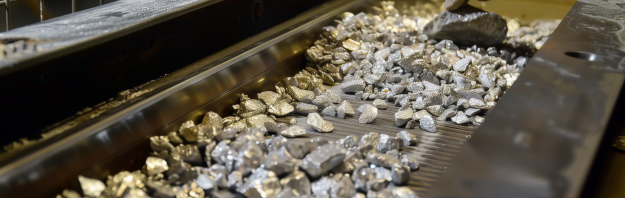