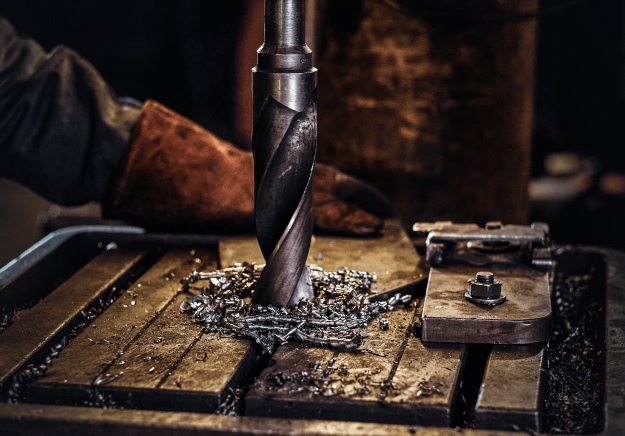
Enhancing the Durability of Metal Surfaces
Conversion coatings play a pivotal role in augmenting the performance and lifespan of metal surfaces. These coatings are protective, non-soluble compound layers that are firmly adhered to material surfaces through chemical or electrochemical reactions. The primary purpose of these coatings is to safeguard a metal substrate from corrosion. However, they can also function as a base layer for additional coatings, improve surface lubrication, or be used to achieve a specific aesthetic.
Speak to our expertsKey Benefits:
-
Understanding Conversion Coating
Conversion coating is a broad term that refers to coatings formed through the chemical or electrochemical treatment of metallic surfaces, resulting in a surface layer containing a metal compound. This process enhances the lifespan and functionality of metal materials by improving attributes such as lubrication and corrosion resistance. They can also enhance the adhesion of subsequently applied coating layers.
-
Conversion Coating vs. Barrier Coating
Conversion coatings and barrier coatings are not the same. Conversion coatings are a type of surface passivation used to modify the surface of a metal, creating a protective metal oxide layer against corrosion and wear. Conversely, barrier coatings act as effective moisture or physical barriers, often applied on metals and ceramics to withstand harsh conditions. While conversion coatings enhance metal surfaces, barrier coatings provide a protective layer against environmental factors and are sometimes applied over conversion coatings for added protection.
-
Conversion Coating vs. Anodizing
Anodizing is a specific type of conversion coating. Conversion coating refers to various processes in which a metal surface undergoes a chemical reaction to enhance its properties. Anodizing, a technique in this category, involves the electrolytic oxidation of metals, usually aluminum, to produce a corrosion-resistant layer.
-
The Role of Conversion Coating
The primary role of a conversion coating is to create a protective layer on a metal substrate that enhances the metal's overall durability and performance. It provides a more suitable surface for painting and bondings.
-
Conversion Coating in Manufacturing
Manufacturers of metal products requiring protection from environmental degradation use conversion coatings to increase their corrosion resistance, and therefore their durability. Conversion-coated products are immersed in or sprayed with a coating solution suitable for the alloy, which reacts with the metal to produce a layer that inhibits corrosion and aids in the adhesion of additional coating layers, such as paint. This treated surface is crucial in several industries. For instance, in the automotive industry, conversion coatings are used on car bodies and parts to protect against rust and corrosion, thereby extending the lifespan of vehicles. In aerospace, conversion coatings are vital for aircraft components to withstand harsh environmental conditions and maintain structural integrity.
-
How Conversion Coatings Work
Conversion coatings function by chemically reacting with the metal surface to create a protective layer. This process varies among the different coating types, which include phosphates, chromates, and black oxide coatings. The specific chemical reactions for each type of conversion coating contribute to enhanced corrosion resistance, improved adhesion for subsequent coatings, and increased overall durability in diverse industrial applications.
-
Conversion Coating vs. Other Types of Coating
Conversion coatings differ from other types of coating primarily because they chemically react with the metal surface, forming a protective layer. In contrast, physical coatings like paints merely create a barrier between the metal and the environment. Protective coatings can be categorized into barrier coatings, inhibitive coatings, sacrificial coatings, and combinations thereof. While non-metallic coatings often utilize polymers, epoxies, and polyurethanes, metallic coatings commonly employ zinc, aluminum, and chromium for corrosion protection. Conversion coatings provide unique chemical modification of the metal surface, enhancing its resistance to corrosion and improving adhesion for subsequent coatings.
At Sona SPEED, we understand the importance of conversion coatings in enhancing the performance and longevity of our specialized electrical machines. Our extensive experience in the design, development, and realization of space-grade motors, such as Brushless DC motors and permanent magnet & hybrid stepping motors, is complemented by our commitment to using conversion coatings to ensure the durability and reliability of our products. We believe in the power of innovation and the pursuit of excellence, and we strive to provide our customers with the highest quality products and services.
Speak to our experts