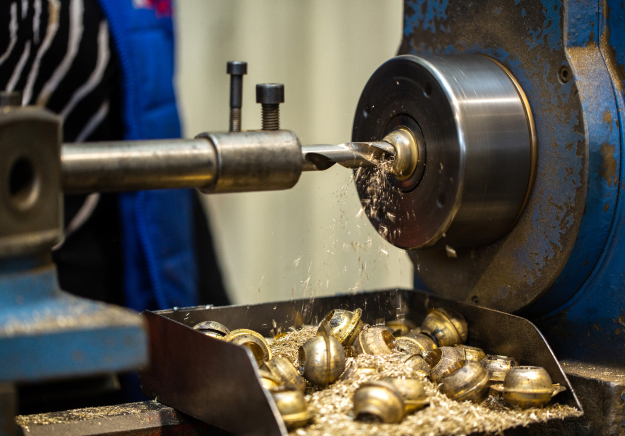
Enhancing Durability and Efficiency with Tin Plating
Tin, a soft, malleable, and silvery-white metal, has been an integral part of human civilization since the Bronze Age. Its versatility and abundance have made it a popular choice for various applications, from the creation of the iconic Tin Man in the Wizard of Oz to the manufacturing of food and beverage containers. At Sona SPEED, we understand the importance of tin in our daily lives and its significant role in the electroplating process. Our Special Power Electronics & Electric Drives division specializes in the design, development, and realization of space-grade motors such as Brushless DC motors and permanent magnet & hybrid stepping motors. We leverage the benefits of tin plating in our manufacturing process to ensure the durability and efficiency of our products.
Speak to our expertsKey Benefits or Points:
-
Tin in Electroplating
Tin plating, also known as "tinning", is a cost-effective process due to the ready availability of tin. It offers excellent solderability and superior protection against corrosion. The electroplating process involves depositing a coating of tin onto the surface of a material using an electrical current.
-
Appearance and Conductivity
Tin plating can produce a whitish-gray color for a dull or matte appearance or a shiny, metallic look for a bit more luster. With a decent level of conductivity, tin plating is useful in the manufacturing of various electronic components. It is also FDA approved for use in the food service industry.
-
Industries Benefiting from Tin Plating
Tin plating finds applications in a wide range of industries, including Aerospace, Food Service, Electronics, Telecommunications, and Jewelry Manufacturing. At Sona SPEED, we harness the advantages of tin plating to enhance the performance and longevity of our specialized electrical machines.
-
Tin Plating Processes
To enhance the tin plating process, tin can be co-deposited (alloyed) with another metal or several metals. Commonly applied tin alloys include Tin-lead, Tin-copper, Lead-tin-copper, Tin-silver, Tin-zinc, and Tin-bismuth.
-
Tin Plating Processes
Tin plating involves three basic types, each relying on the deposition of an electrolytic tin solution onto the surface of a metal object:
Barrel Plating
Used for plating smaller parts, it involves placing the objects in a specially constructed vessel, known as a barrel. The barrel slowly rotates while immersed in the electrolytic plating solution.
Rack Plating
Preferred for plating tin on larger or more delicate parts, it involves hanging the objects on a rack and immersing them in the plating solution.
Vibratory Plating
Used for delicate parts, it involves placing the parts in a basket equipped with metal buttons that also contains the electrolytic plating solution.
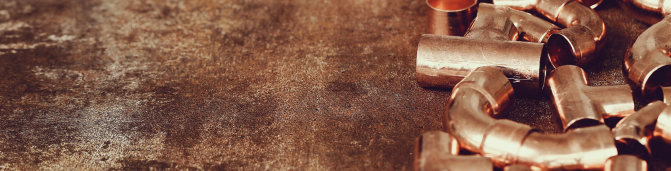
At Sona SPEED, we are committed to leveraging the best practices in tin plating and tin alloy plating to deliver high-quality, durable, and efficient special electrical machines. Our expertise and experience in the field ensure that our products meet the highest standards of quality and performance.
Speak to our experts